The Ultimate Guide to Tooling for Injection Molding
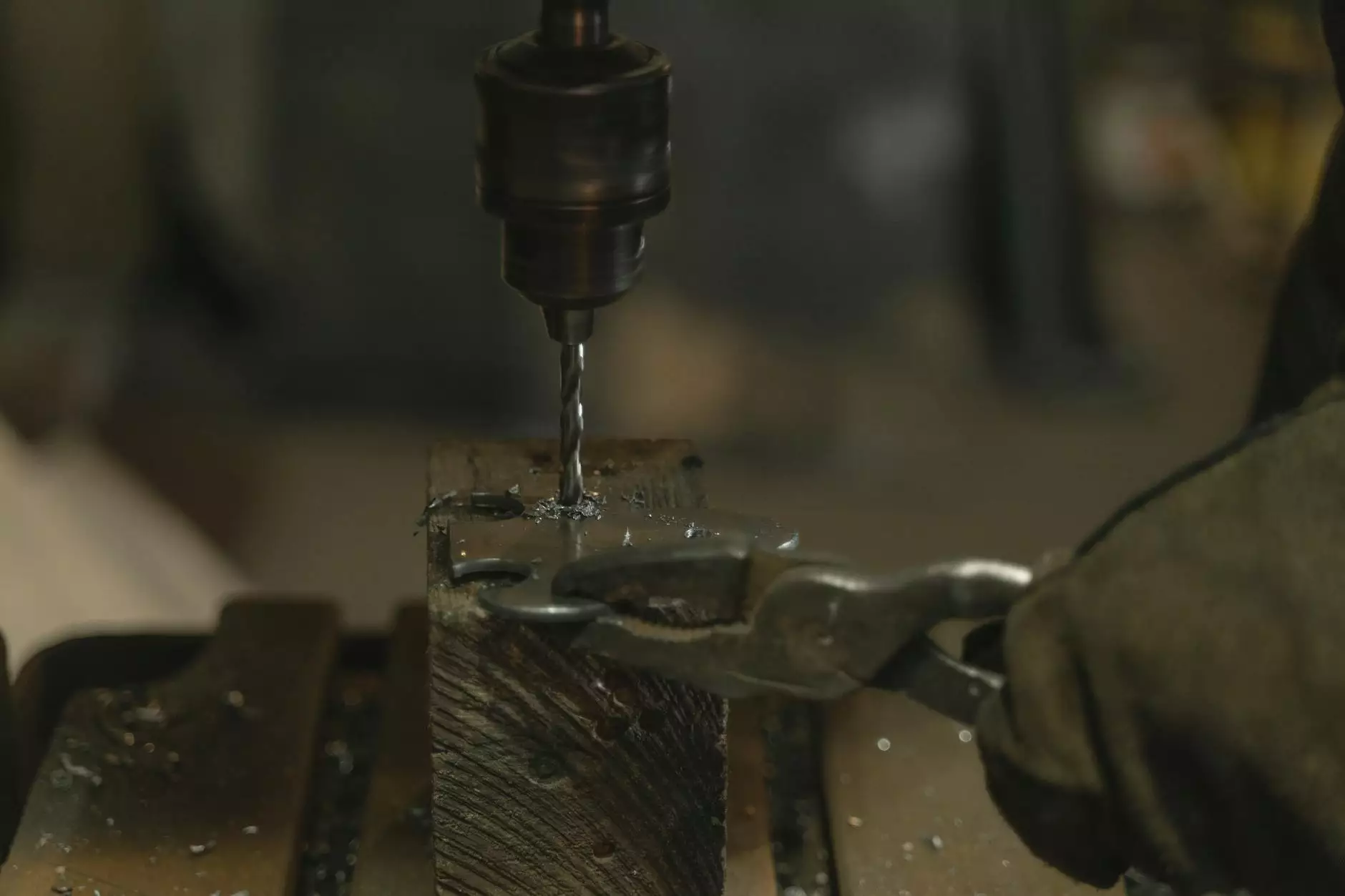
In the realm of manufacturing, tooling for injection molding stands as a cornerstone of efficient production processes and product quality. This guide aims to delve deeply into the significance, techniques, and innovations surrounding this essential aspect of industry, particularly within the category of metal fabricators.
Understanding Injection Molding and Its Importance
Injection molding is a widely used manufacturing process that involves the injection of molten material into a mold to create complex shapes and components. This process is pivotal in various sectors, including automotive, consumer goods, and industrial applications. The importance of injection molding lies in its ability to produce high volumes of parts that are not only consistent in quality but also economically viable.
What is Tooling in Injection Molding?
Tooling, in the context of injection molding, refers to the design and manufacture of the molds used to create plastic or metal parts. The tooling process is crucial because high-quality molds directly influence the efficiency of production, the consistency of the final products, and the overall manufacturing costs.
The Components of Injection Molding Tooling
- Mold Design: This is the initial phase where the specifications and dimensions of the end product are translated into a mold design.
- Material Selection: Choosing the right materials for the mold construction is vital, as it affects durability and performance.
- Mold Manufacturing: This involves precision machining processes to create the mold based on the design specifications.
- Mold Maintenance: Regular maintenance ensures the longevity and effectiveness of molds, thus optimizing the injection molding process.
The Role of Metal Fabricators in Tooling for Injection Molding
Metal fabricators play a crucial role in the tooling process, providing the expertise and technology required for producing high-quality molds. Their capabilities include:
Advanced Machining Techniques
Metal fabricators utilize state-of-the-art machinery and processes such as CNC machining, EDM (Electrical Discharge Machining), and precision grinding, which are vital for creating intricate mold designs. These techniques ensure that each mold component meets exact specifications, resulting in parts that fit and function properly.
Custom Tooling Solutions
Every injection molding project may have unique requirements. Custom tooling solutions developed by skilled fabricators cater to specific industry needs, enhancing productivity and reducing scrap rates.
Quality Control
To ensure that molds meet stringent quality standards, metal fabricators implement rigorous quality control measures throughout the tooling process. This includes:
- Dimensional Inspection: Measuring mold components to verify that they meet design specifications.
- Surface Finish Testing: Ensuring that surfaces are finished to the required texture for optimal performance.
- Geometric Inspection: Verifying that the mold's geometry is precise to ensure its functionality.
Innovations in Tooling for Injection Molding
As industries evolve, so do the technologies and methodologies associated with tooling for injection molding. Important innovations include:
Rapid Prototyping
Rapid prototyping allows for faster mold design iterations by employing techniques like 3D printing. This accelerates the development process, enabling manufacturers to test designs quickly and make necessary adjustments before full-scale production.
Smart Molds
Integration of smart technologies into molds, such as sensors that monitor temperature and pressure, is transforming the injection molding landscape. This technological advancement allows for real-time data collection and process adjustments, leading to improved product consistency and reduced waste.
Environmental Sustainability
There's a growing emphasis on sustainable practices in tooling for injection molding. Metal fabricators are now adopting eco-friendly materials and processes, minimizing waste, and improving energy efficiency during production.
Choosing the Right Fabricator for Injection Molding Tooling
Selecting the right partner for your tooling needs is crucial for the success of your injection molding projects. Here are some factors to consider:
Experience and Expertise
Look for a metal fabricator with a proven track record in tooling for injection molding. Experience in your specific industry can greatly impact the quality of their work.
Technology and Equipment
Modern machining equipment and technologies can significantly enhance the accuracy and quality of your molds. Ensure that the fabricator uses advanced technology in their manufacturing process.
Customer Support
Effective communication and support throughout the project are essential. A fabricator that provides clear timelines, updates, and responsive support can help mitigate any potential issues.
Conclusion
In conclusion, tooling for injection molding is a critical component of efficient manufacturing processes, especially within the context of metal fabrication. Understanding the intricacies of mold design, selection, and maintenance is vital for companies looking to enhance their production capabilities and product quality. With the continued advancements in technology and a focus on sustainability, businesses can expect to see significant improvements in the injection molding process for years to come.
For businesses in need of expert tooling services, DeepMould.net stands out as a leader in the field. Committed to quality and innovation, they offer a comprehensive range of services tailored to meet the unique needs of the injection molding industry.
Embrace the future of manufacturing today by understanding and investing in quality tooling for injection molding.